PRESSLER® ZINC COATING HOT STAMPING TECHNOLOGY
1.Current Issues in Hot Forming (HF) & Motivation |
|
2.Pressler Zinc Coating HF Technology |
|
3.Pressler Zinc Coating HF Performance |
|
4.Next Steps |
|
5.Summary |
Current Issues in Hot Forming (HF) & Motivation
Current Issue 1: Poor Anti-Corrosion on Al-Si Coated Parts
Statement: Al-Si coated hot stamping parts have poor corrosion resistance on both cosmetic and perforating. Corrosions start at weld line, surface scratch from forming, trim edge, and any area not covered by E-coating.
![]() |
![]() |
![]() |
![]() |
Al-Si COATED B-PILLAR |
AFTER 48H NEUTRUAL SALT SPRAY (NSS) |
TAILOR B-PILLAR AFTER 16H NSS |
AFTER 240H NSS |
Current Issue2:Low Bending Angle of Al-Si Coated Parts
Statement: Al-Si coated hot stamping parts have low bending angles
SEM of Al-Si coating after hot stamping (500 times)
Carbon content distribution
Table 1 Bending angles of AL-Si coated 22MnB5 plates.“patent:CN 108588612A”
Coating types |
Thickness |
Coating thickness |
Bending Angle 1 |
Bending Angle 2 |
Average |
Al-Si |
1.5mm |
30-50um |
50.8° |
52.7° |
51.8° |
OXIDE SCALE (>5um)
Current Issue 3: High Cost on Al-Si Coated TWB
Statement: : Al-Si coating needs to be removed before welding
SEM of section of TWB of Al-Si coated blank Picture from VW TL4225
It is generally not allowed to appear brittle fe - Al phase in the weld line of al - Si pre - coated laser butt welding parts
Current Issue 4: Shorten Life of Furnace Rollers on Al- Si heating
Statement: Melting Al-Si coating
during heating
will damage
the surface
of ceramic
rollers.
Contamination of ceramic roller by melting Ai-Si coating
Under high temperature, the coating melts and continuously diffuses inside the ceramic roller, leading to the hump formation or even fracture of the ceramic rollers. Therefore it reduces the service life of the rollers
Main Issues in Al-Si Coating and Zinc Coating Indirect PHS Parts
Al-Si Coating PHS Parts
Zinc (Zn) Coating Indirect PHS Parts
Poor corrosion resistance capability
Crack in coating layer or even in substrate
Shot blasting needed to remove Zinc Oxide (ZnO)
High cost on TWB
High cost on Indirect PHS
Liquid Al-Si contamination on furnace roller
Vapor or liquid Zinc contamination on furnace
Pressler Vacuum Hot Forming Zinc-Coated Parts
Manufacturing Process :
![]() |
![]() |
![]() |
![]() |
![]() |
Laser Blanking |
|
Vacuum heating |
|
Hot forming |
|
|
|
|
![]() |
![]() |
![]() |
![]() |
![]() |
![]() |
Product |
|
Electro-Galvanizing |
|
Laser cutting |
Pressler Third-Generation Hot Stamping Technology
Heating Process:
Pressler Vacuum Heating Hot Forming Try-Out Line
Vacuum Heating Hot Forming: Oxide Layer
OXIDE LAYER THICKNESS< 2μm
Zinc Coating Uniformity
电镀锌挂架
The coating tolerance range of the electroplating process is 7-13um
Three-Point Bending Angle of Zinc Coated Parts
Coating Type |
Material Thickness |
Coating Thickness |
Bending Angle 1 |
Bending Angle 1 |
Bending Angle 1 |
Bending Angle 1 |
Bending Angle 2 |
Bending Angle 3 |
Electro-galvanized Plate |
1.5mm |
7-13um |
80.65° |
81.77° |
76.44° |
81.21° |
76.11° |
67.6° |
![]() |
![]() |
![]() |
TEST EQUIPMENT |
3-POINT BENDING ANGLE SAMPLE |
DROP TOWER TEST |
Cyclic Corrosion Resistance Performance
Testing Standard: AA-0224:2018 Cyclic Corrosion Test, DIN EN ISO 11997-1, Cycle B
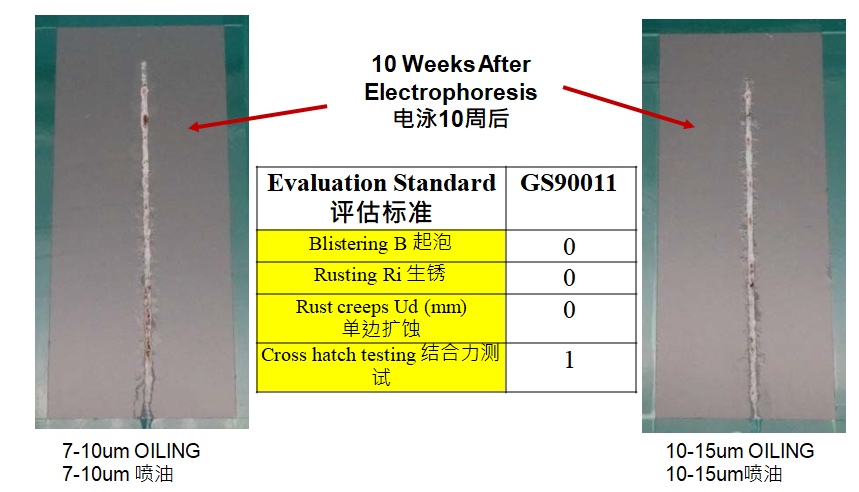
氢含量测试报告
Heat treated A1
Galvanized samples [ppm]
Average
[ppm]
Deplated samples [ppm]
Average
[ppm]
A1-1
0.29
0.33 士 0.04
A1-2
0.37
A1-3
0.08
0.08 主 0.005
A1-4
0.08
A1-5
0.07
Non.heat treated A2
Galvanized samples [ppm]
Average
[ppm]
Deplated samples [ppm]
Average [ppm]
A2-1
11.62
13.17 士 1.55
A2-2
14.71
A2-3
0.24
A2-4
0.16
80th materials were analyzed after deplation as well as in the as-delivered galvanized condition. Deplating was performed in 18.5% HCI + 5 g/
l
Hexamethylenetetramine
(cor rosion inhibitor). AII analyses were carried out by means of Thermal Desorption Spectroscopy (TDS) at an isothermal temperature of 300 oC.
Hydrogen Embrittlement Test
U-Bend Specimen U 型折弯样品
(SEP 1970)
Low Cost and Advantages
Low Cost Factors :
Uncoated 22MnB5 material = lower cost
TWB of uncoated blank = lower cost
Vacuum heating = same cost as Atmosphere Protection Heating
Zinc Plating and Tempering = same cost as Al-Si coating
Advantages:
Common tailor welding
Pressler Summary
Pressler technology on hot stamping parts provides automotive OEMs a
new solution on reducing cost and enhancing corrosion resistance